Unlocking the Advantages: 5 Key Benefits of Pre-Engineered Metal Buildings
Exterior shell of PEMB – building ready to have roof panels installed.
In the construction industry, PEMB is an acronym that stands for pre-engineered metal building. If you’re wondering what this means, the name says it all:
Pre-engineered metal buildings are structural steel buildings made from parts that are prefabricated off site and then assembled at their final location.
PEMBs were initially used for airplane hangars and grain storage facilities in the 1930s when they first started gaining popularity. Now, nearly one hundred years later, PEMBs are being utilized for a variety of structures. Some of which include retail spaces, office buildings, manufacturing plants, and warehouses.
You may be wondering, why the surge in popularity?
For starters, PEMBs are more cost efficient to build, take less time to assemble, and are highly versatile. Not only that, but they’re also more durable and require less upkeep. Because of this, they’ve become a preferred choice in large-scale commercial construction.
Here’s an in-depth look at each of the 5 key benefits of PEMBs:
01. Cost Efficiency
One of the most notable benefits of choosing a PEMB over a traditional building is that they are significantly less expensive to build.
There are several factors that contribute to this, which include:
Reduced labor costs - when a client selects a pre-engineered metal building for their project, the manufacturer is involved in the initial design stages so they can develop the exact steel fabrications the building needs off site. This reduces the labor traditionally required and the construction site costs overall.
Lower HVAC cost - each of these fabrications are equipped with proper insulation so it requires less energy to maintain a comfortable indoor temperature, ultimately reducing the cost of heating and cooling.
Smaller Insurance Premiums - steel buildings are better equipped to resist fire, wind, water and other natural elements that could damage a building’s structural integrity. With that being said, since most insurance premiums are based on the likelihood of damage, PEMBs often have significantly lower insurance premiums in comparison to conventional buildings.
Lower Maintenance Costs - Since they are less susceptible to natural damage, steel buildings don’t require as much maintenance. They are also resistant to pests that could cause damage to its structure, like termites. Because of this, their maintenance costs tend to be far lower than buildings made of other materials.
02. They Take Less Time to Build
Constructing a building using traditional methods can take months, and, in some cases, years to complete. Pre-engineered metal buildings, on the other hand, can be assembled fairly quickly once all of the materials have been delivered to the job site.
Since all of the building materials are in one place and ready for use, the delegation and execution of specific duties is much more streamlined, making it easier to adhere to the project’s timeline. Essentially, because all of the building’s components are coming from one supplier, you can dramatically improve the rate at which the building is assembled. This is made possible through:
A clear vendor management system
Material accuracy and compatibility - since they’re all designed by the same manufacturer they will all feature the correct measurements.
Build materials are made in compliance with the specific building codes being enforced in that particular area
Minimal site disruption
Timely delivery of all components before the project commences
Early access to the site to set up the post-erection trades
03. They Are Highly Customizable
Pre-engineered metal buildings can be tailored to fit the client’s specific needs. Engineers and fabricators can collaborate to create a design that suits various types of structures including industrial, commercial, residential storage, warehouses, or agricultural buildings.
Here are few of the customizations that can be made to a PEMB:
They can be designed to meet specific, local code requirements.
They can be designed with taller ceilings to accommodate tall racks and shelves.
PEMBs can be outfitted with various doors, windows, roll-ups, and other features to suit the specific needs of a particular business.
You can customize framing options featuring a clear span, modular auxiliary, and single-slope.
Additionally, they can be designed with a variety of different roof styles. The most common roof style for PEMBs is the gable roof, but other options include the hip roof and the gambrel roof.
04. Extreme Durability
Pre-engineered metal buildings are made from steel, which is one of the strongest materials out there. This allows them to withstand even the harshest of weather conditions, making them far more resilient than other structures. Since they are more resistant to damage caused by natural elements, they tend to be the most reliable choice.
05. They Are More Sustainable to Maintain
As we mentioned before, pre-engineered metal buildings require far less maintenance than traditional buildings. They can often go decades with little to no maintenance because they are thoroughly insulated, extremely durable, and more resistant to elemental damage.
Following installation of banding and scrim paper, insulation and roof panels are installed.
Now that you’re aware of the benefits of pre-engineered metal buildings, what can you expect from a subcontractor that specializes in PEMB Erection?
Think of a PEMB like a gigantic lego set, except subcontractors are using sheets of metal and steel beams. Each piece has a specific place and purpose. So, in the construction world it’s a race against time to see how fast a team can assemble the giant set.
SCC specializes in PEMB erection as well as concrete, steel stud framing, and carpentry. Anyone working with us on a PEMB project can expect to be using/around large machinery; cranes, reach man baskets, scissor lifts, forklifts etc. Most of the time a PEMB sits on top of some sort of concrete – whether it be a slab on grade or large footing pads – so there is also an opportunity to form, reinforce and pour the foundation for the building.
Erecting a PEMB with SCC is a rewarding and challenging task. Our admin and estimating team create a work plan of hours for each task of the erection process. That work plan is coordinated by the onsite Foreman who sets schedules, inspections and man-power in conjunction with the work plan. SCC’s experience in concrete as well as PEMB erection and framing gives us an experience advantage in how to problem solve efficiently in any given situation.
If you like working outside, using your hands, solving complex problems, and are motivated to see a goal through to its completion, you’ll enjoy working with us on the PEMB opportunities we have. If you’re interested in learning more, reach out to us. We’d love to talk with you.
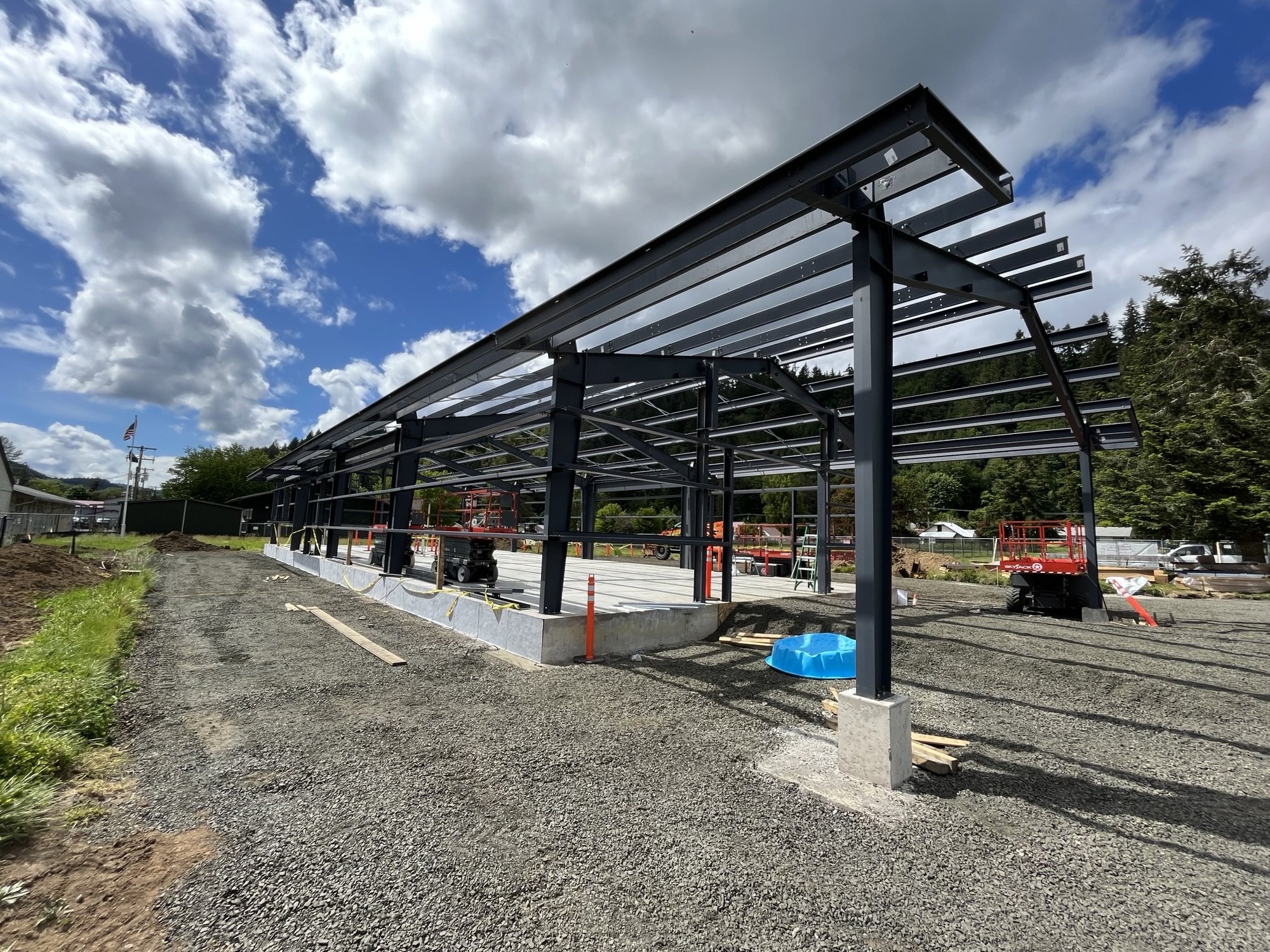
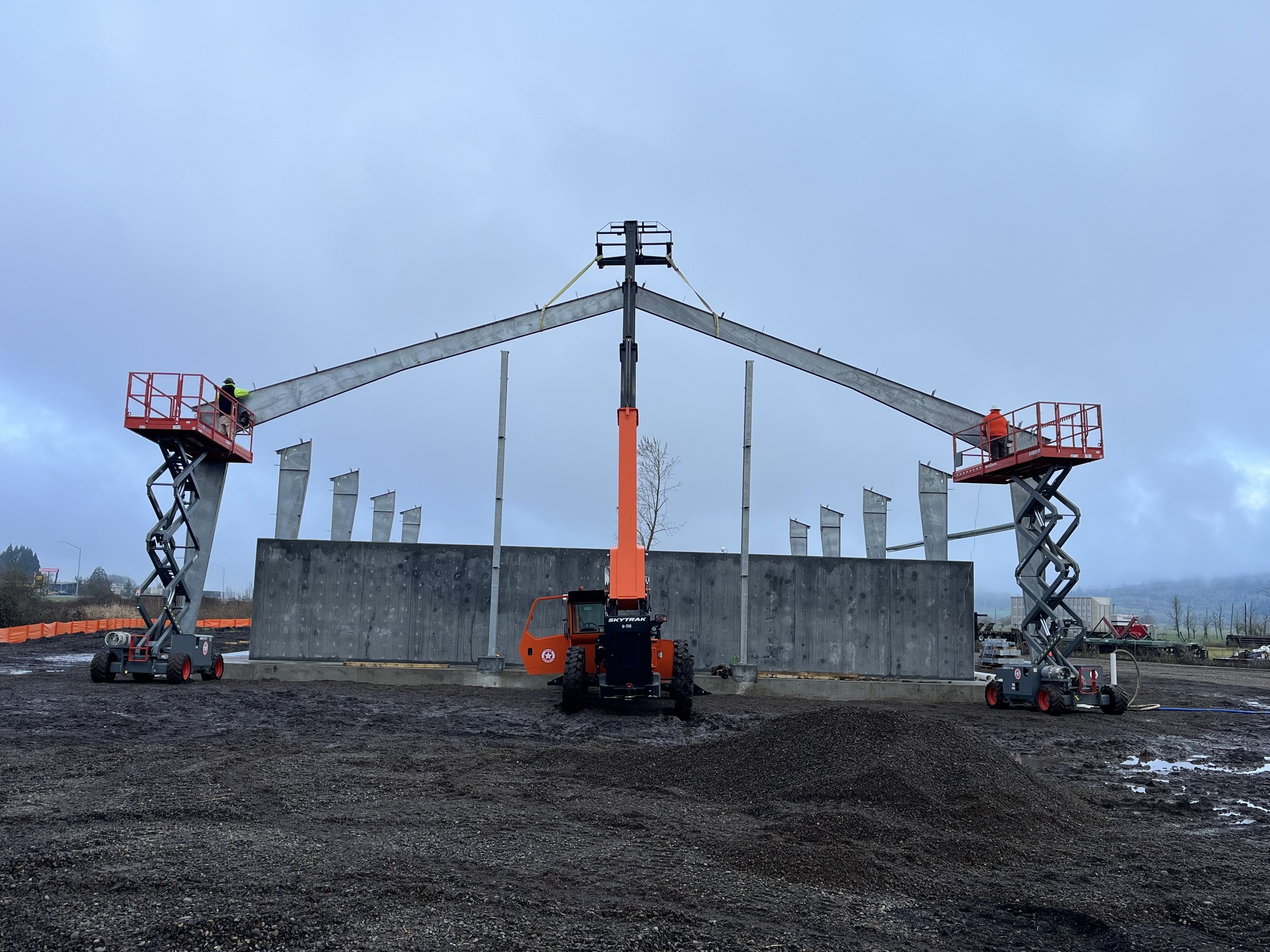
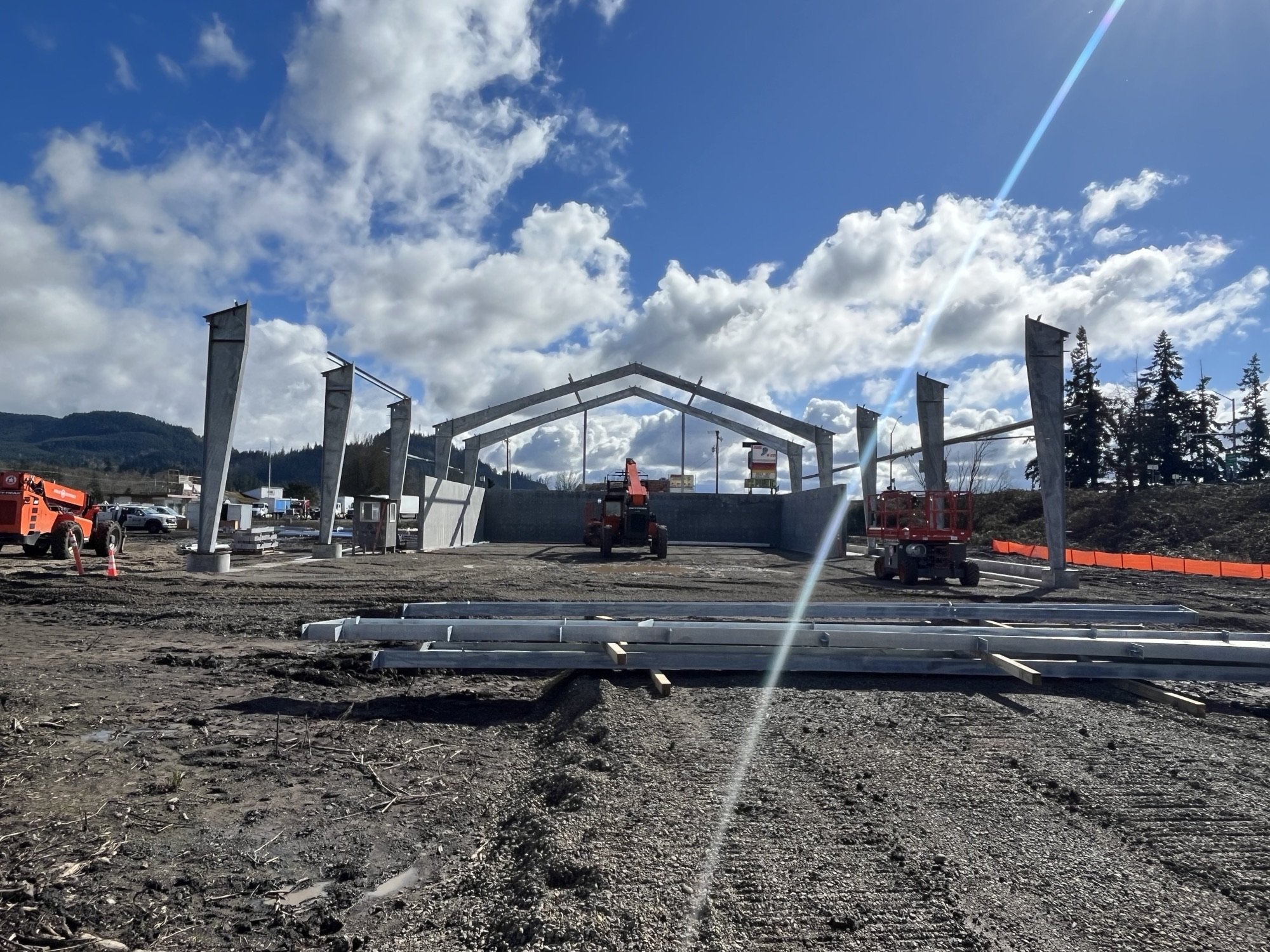
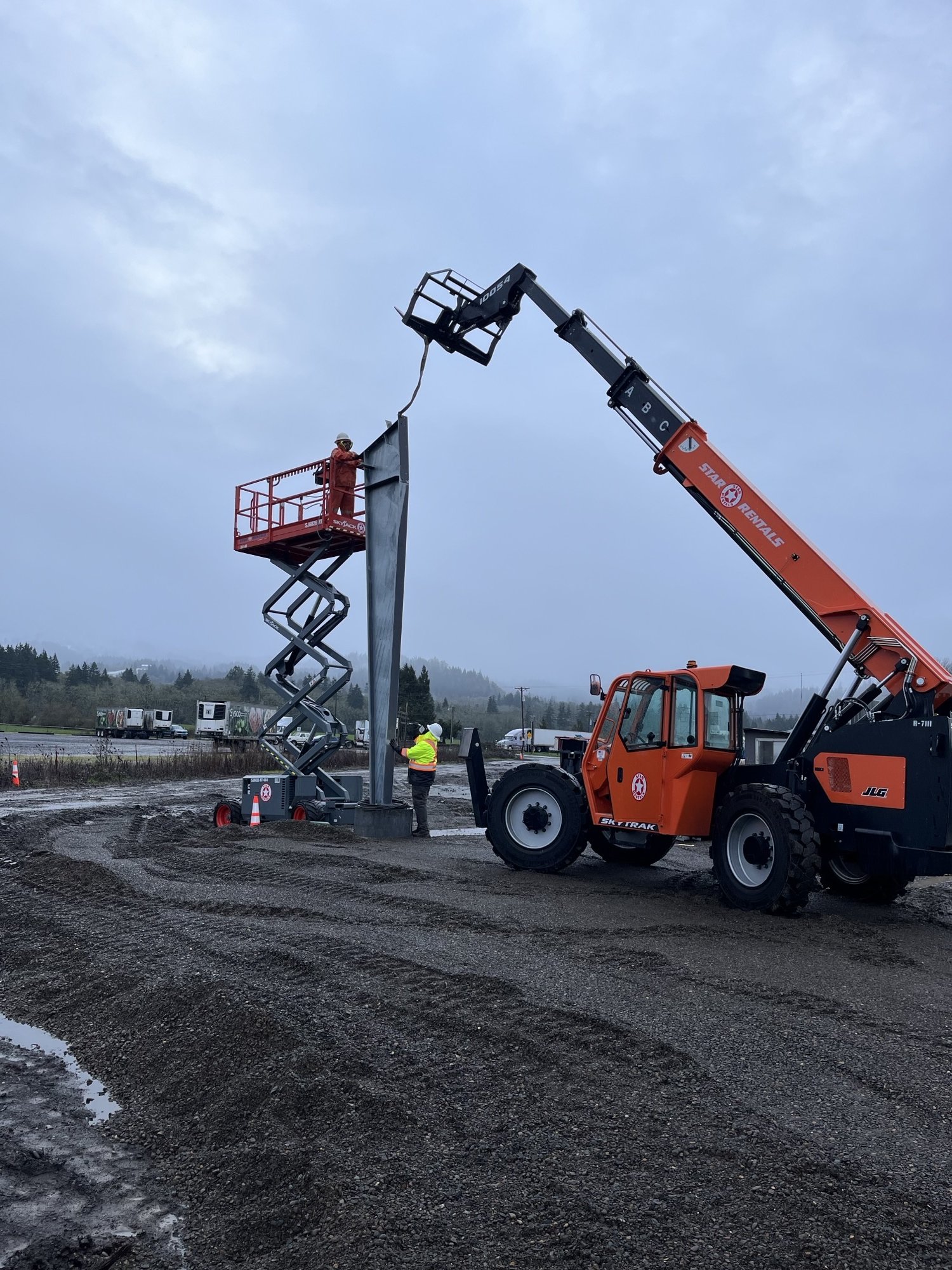
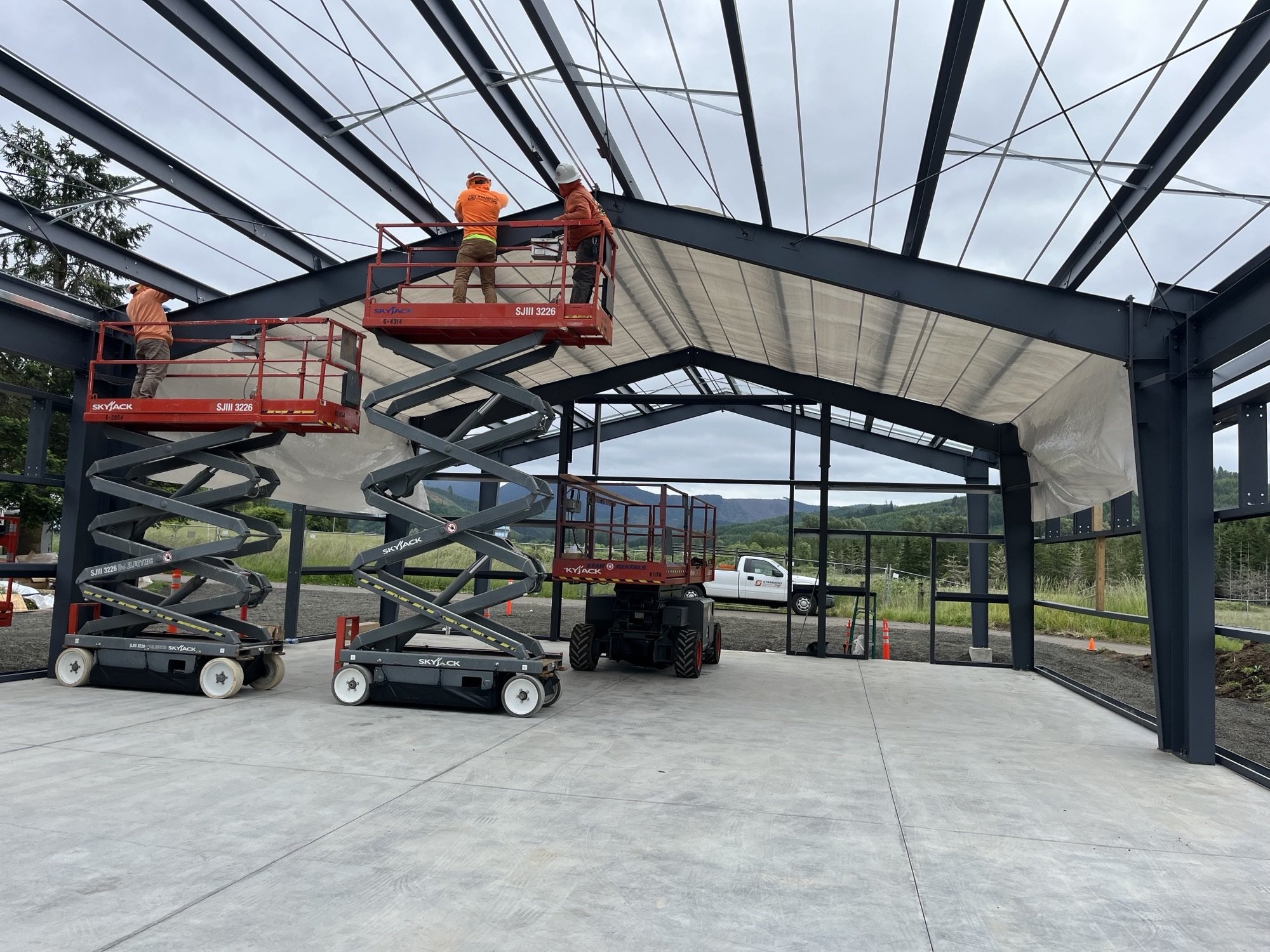
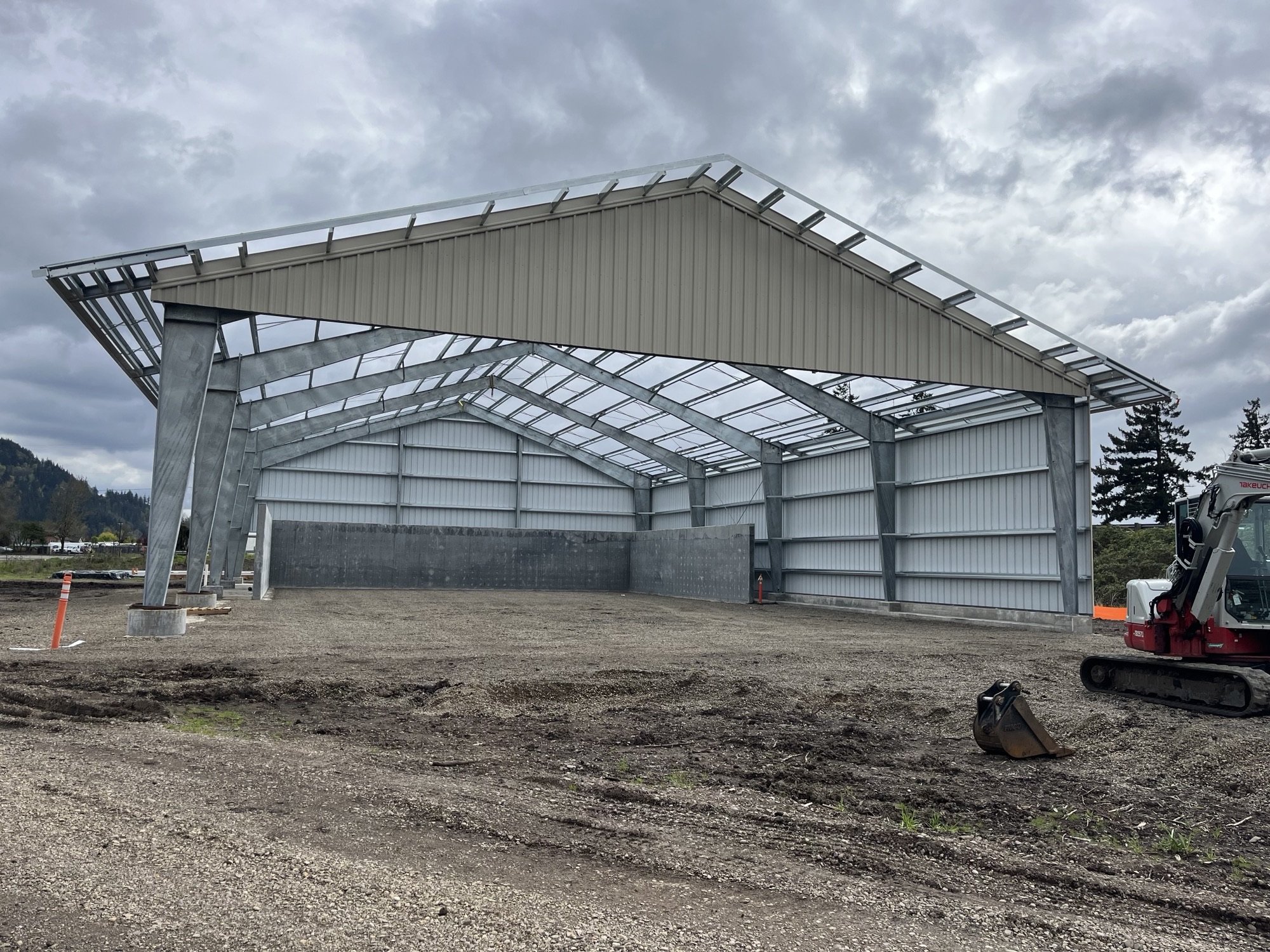
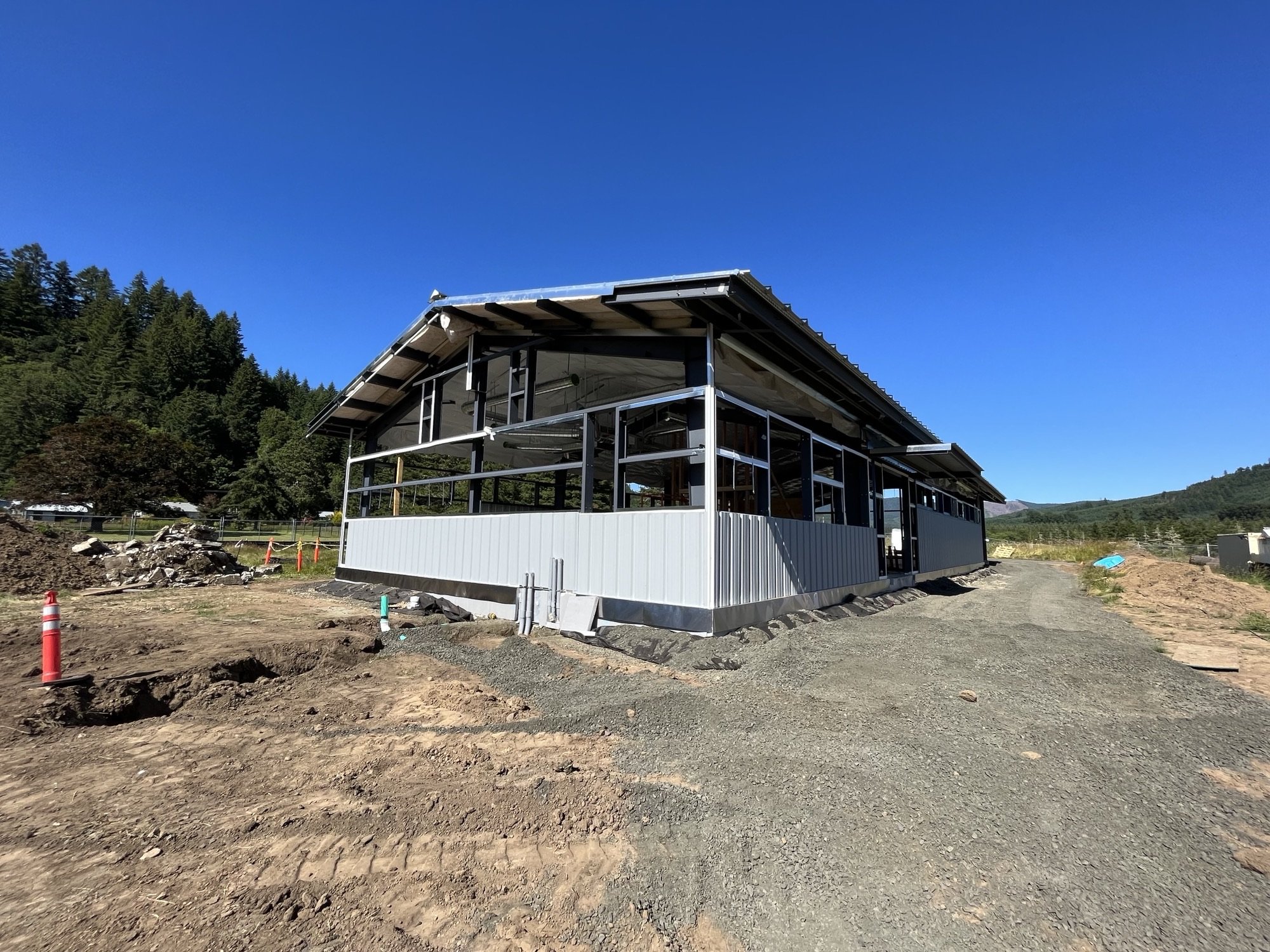